China’s coal industry relies heavily on underground mining. As of 2022, this method is employed by 92% of the nation’s coal mines, contributing to 82% of domestic coal production.
High demand for coal has driven Chinese coal companies to leverage intelligent mining technology. According to the National Mine Safety Supervision Bureau of China, there are over 1,300 intelligent mines in China.
One of these intelligent mines is the Wangjialing coal mine. Located in Shanxi Province, it produces approximately 16,000 tons of coal per day, roughly equivalent to an annual output of six million tons. Conveyor belts known as scraper conveyors are essential to transport coal to the surface. Each conveyor may stretch up to 20 kilometers, consisting of a series of chains that are three to four kilometers long.
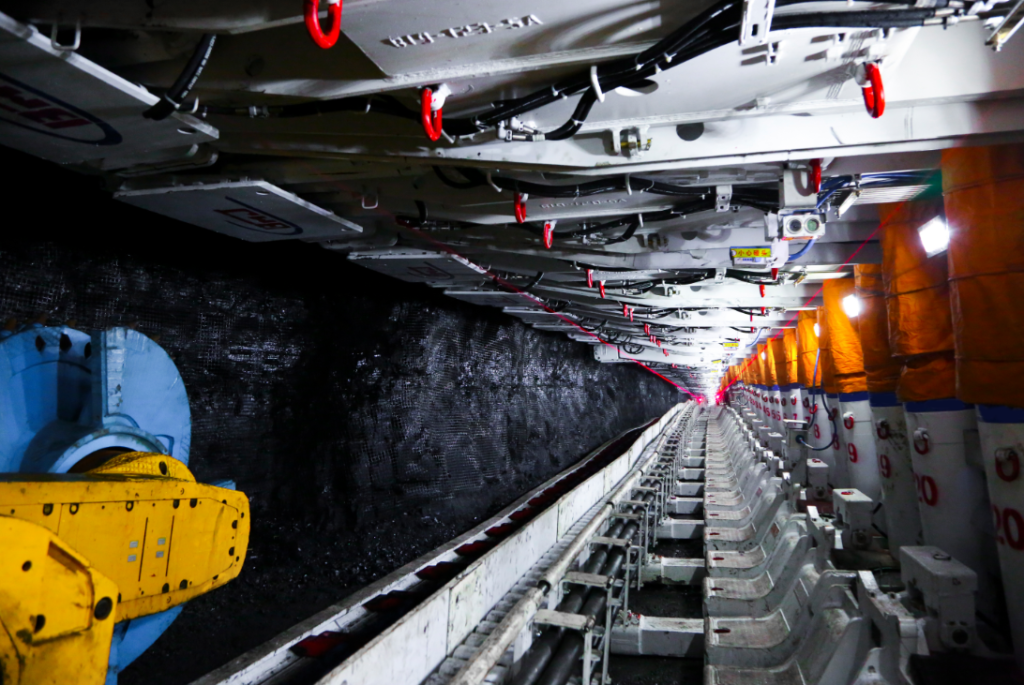
Under constant heavy loads, scraper conveyors can deform or even break, affecting the mining process. Replacing a deformed chain takes around 30 minutes, but if a chain breaks, dismantling and reorganizing the entire conveyor system could take 20 hours or more. The challenge lies in detecting deformations before they lead to breakdowns.
Previously, the Wangjialing Coal Mine employed manual inspection methods, which required approximately 200 specialized maintenance personnel to descend underground for inspections. This approach was costly and posed significant risks to safety, prompting the mine to seek alternatives.
It eventually collaborated with Lenovo to develop a 3D visual recognition system for scraper conveyors. By installing high-resolution 3D cameras atop each scraper conveyor, images of the conveyor chains can be captured continuously and in real-time to assess their condition. These cameras are also equipped with cleaning devices to adapt to the dusty mine environment.
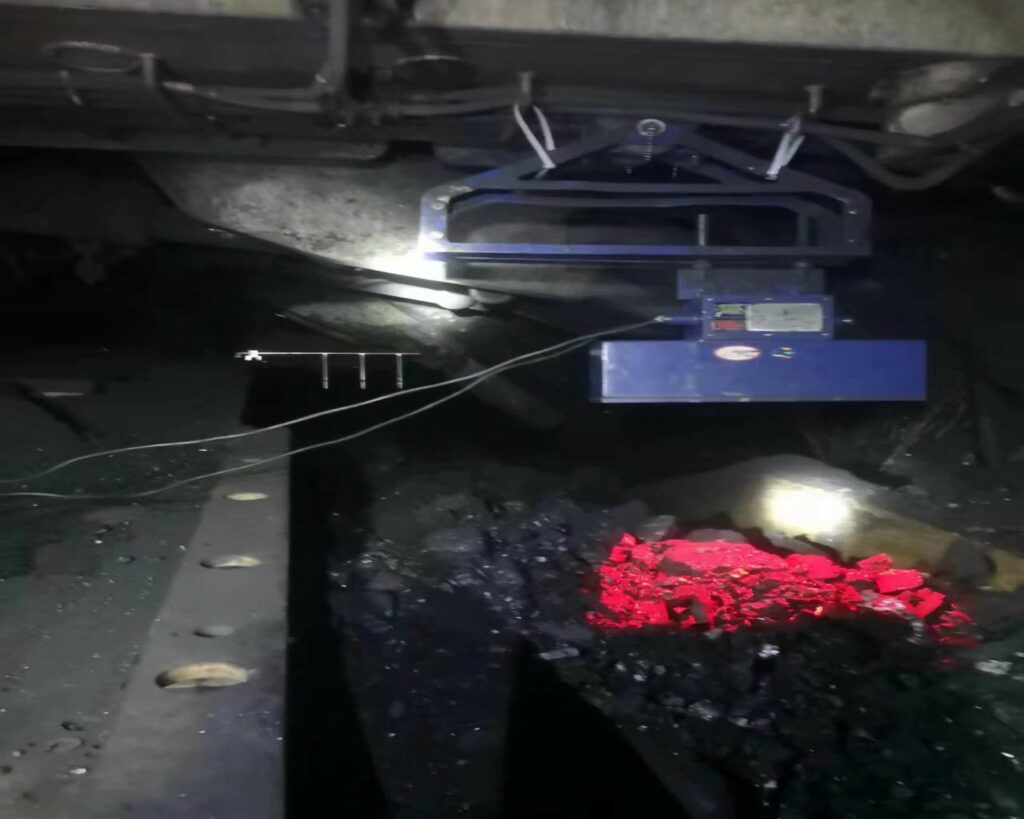
Equipped with low-light sensing and artificial intelligence-based image recognition capabilities, Lenovo’s system can capture and analyze 3D depth images in dark environments, allowing it to detect abnormalities of conveyor chains up to a one-millimeter precision.
The accuracy, efficiency, and safety of maintenance operations at the Wangjialing coal mine have significantly improved since the adoption of Lenovo’s solution. Defect detection coverage and daily maintenance coverage have risen above 95% and 99% respectively. The time taken to respond to anomalies has also been cut by 80%, and the average daily downtime caused by line stoppages has been reduced to two minutes, boosting the mine’s productivity.
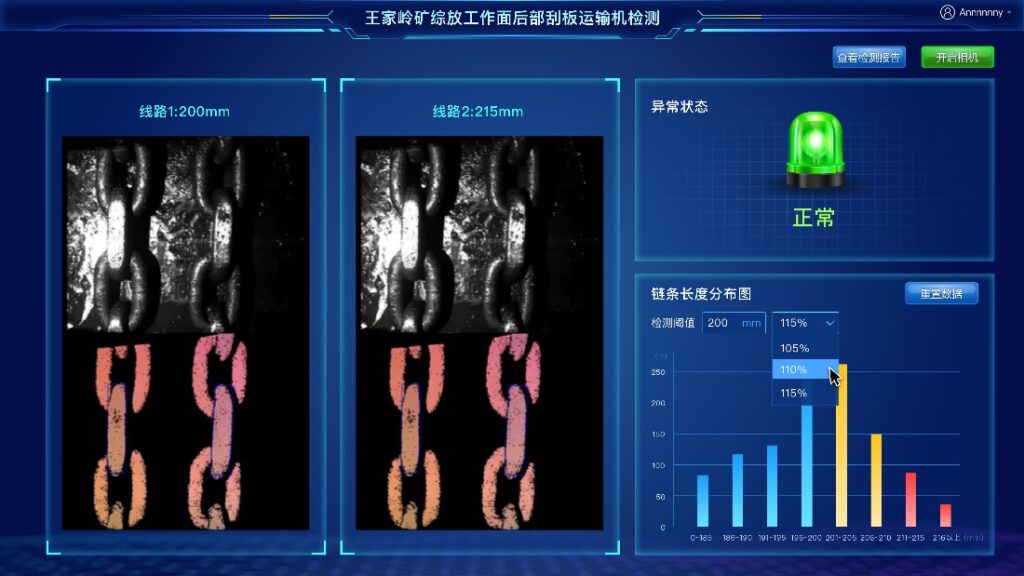
By automating the inspection process, the mine’s maintenance team now spends 90% less time underground. Manual inspection of scraper conveyors is no longer required, and maintenance workers only descend underground when repairs are necessary.
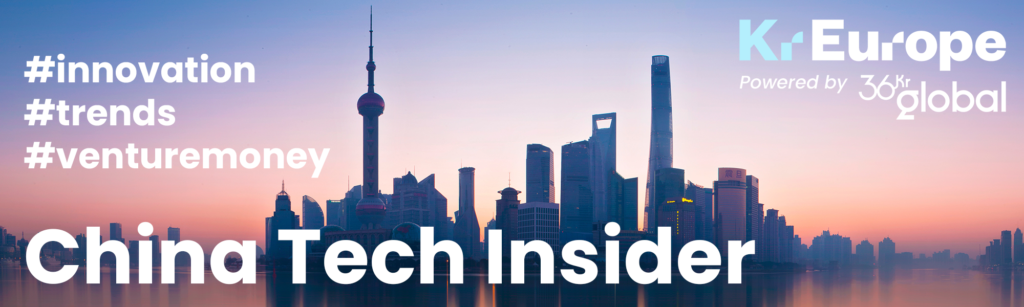